As pressure to act on climate change ramps up, many businesses are grappling with the potential costs of upgrading diesel plant to electric. But HVO fuel can offer a quicker, more cost-effective route to decarbonisation.
Contents - Quick Navigation
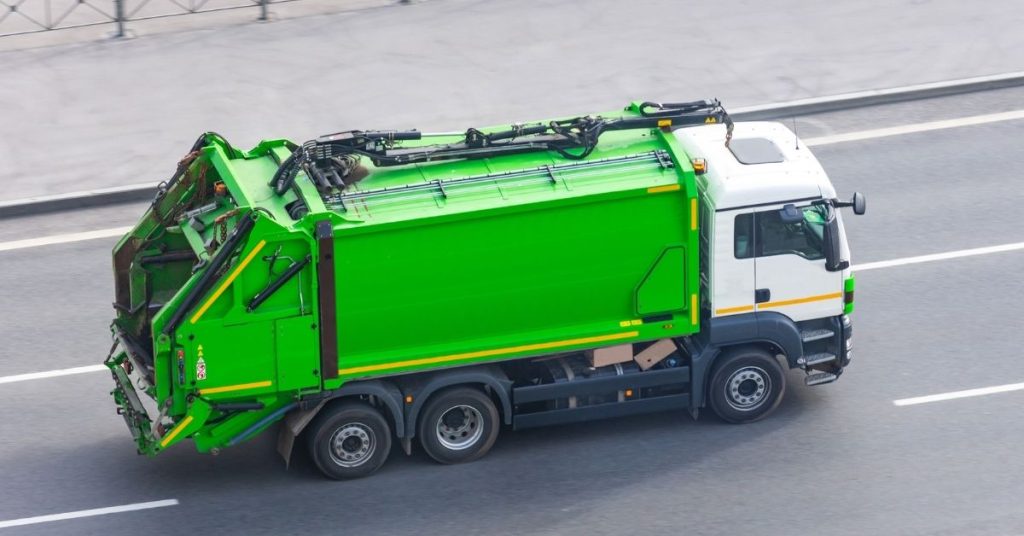
This guide summarises:
- The greenhouse gas emissions of using Hydrotreated Vegetable Oil (HVO) compared to electricity
- How HVO can spread out the costs of decarbonising your assets
- Why going electric too early may be counterintuitive
Companies are under increasing pressure to cut their greenhouse gas emissions, and fossil fuels like diesel are at the top of the priority list. For most applications, businesses have two options: go electric or switch to an alternative fuel.
Prema HVO is a low carbon diesel alternative made from 100% waste cooking oil. The material in the fuel itself can be considered carbon-neutral; the only net greenhouse gas emissions are those produced during the manufacturing process and transportation.
As a result, the ‘carbon intensity’ of Prema HVO (the greenhouse gas emissions per unit of fuel) is around 13 times lower than regular diesel. But how does it compare to going electric?
HVO fuel vs. grid electricity
The UK has made rapid progress in transitioning to renewable power sources like wind and solar, which has significantly lowered the carbon intensity of electricity on the grid. We all look forward to the day when the electricity we use is completely carbon-free. However, it will still be many years before this happens.
The carbon intensity of UK electricity currently averages above 100g CO2e/kWh (carbon dioxide equivalent per kilowatt hour). In contrast, Prema HVO produces just 32g CO2e/kWh. On days when there is little sun or wind, electricity can even spike to 100 times the carbon intensity of HVO.
In other words, while switching to electric plant may be a viable option in the long-term, HVO provides maximum impact today and will continue to outperform electric plant on an emissions basis for many years.
2# CAPEX vs. OPEX
HVO also offers immediate impact at comparatively minimal cost. Electrifying diesel equipment requires multi-million-pound levels of investment in new plant and power infrastructure. In some cases, the technological solutions required are not even available on the market yet.
Switching to HVO requires no capital investment whatsoever; no new equipment or infrastructure is required. The switch is simply an operational cost that can be designed around your budget, allowing you to spread the cost of decarbonisation over a longer period without delaying emission reduction.
3# Upgrading vs. extending
When it comes to appraising new investments in plant and equipment to support decarbonisation, it is wise to take a whole-lifecycle approach. Every new asset comes with an ‘embedded’ carbon footprint – the greenhouse gas emissions that were emitted in the process of making it in the first place. The embedded carbon of vehicles and plant (especially electric models with heavy batteries) makes up a significant portion of the carbon footprint of their full lifecycle.
Replacing assets before the end of their operational lifespan can therefore be a counterintuitive strategy when it comes to total greenhouse gas emissions. It is often much more effective to extend the lifespan of large diesel equipment as much as possible while reducing their emissions in operation.
Switching to HVO does just this; enabling you to maximise the lifespan of your existing plant while making significant strides in cutting your emissions from day one.