This article will introduce FAME, explore how it affects your business, and discuss how you can manage or avoid these issues.
The addition of FAME (biodiesel) into regular diesel and gasoil has resulted in a number of frequent issues – affecting all areas of the fuel supply chain. FAME based biofuel components are prevalent across the UK fuel market. In accordance with updated government regulation, these biofuel components are now widely blended into both road fuel and non-road gasoil.
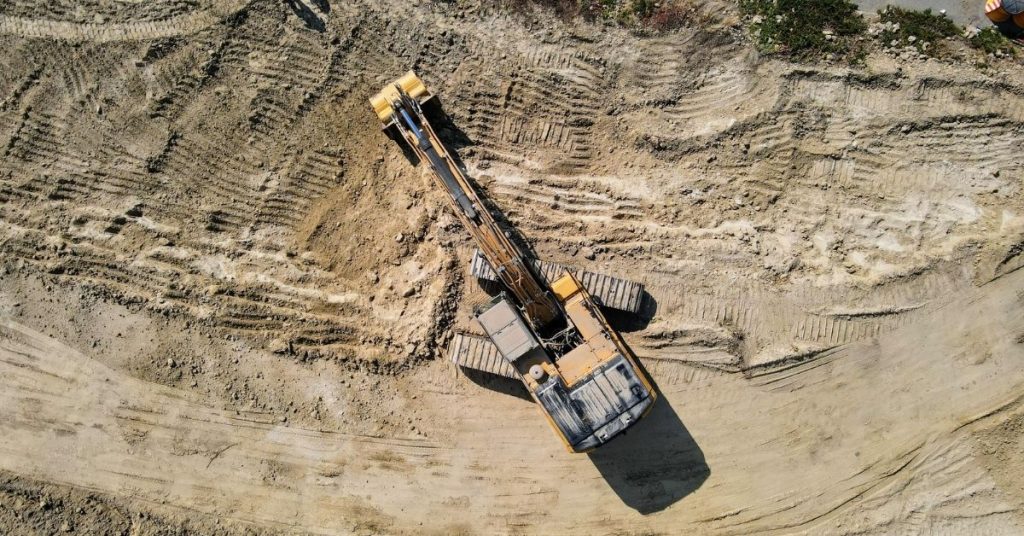
If your business stores, transports or combusts fuel-oil, it is vital to understand the problems resulting from FAME content and how they are best managed.
This guide will help you to:
- Reduce asset downtime
- Limit unexpected maintenance costs
- Avoid unnecessary disposal of contaminated fuel products
1# What is FAME?
FAME is a generic chemical term for renewable biodiesel which has been created through a process known as transesterification. FAME (or Fatty Acid Methyl Esters) biodiesel is created from vegetable oils or animal fats.
The Renewable Transport Fuels Obligation (RTFO) is periodically implementing tougher biofuel targets across the UK transport sector. Currently, fuel producers are obliged to blend regular diesel and gasoil with approximately 7% FAME. This is set double in the next few years.
Thanks to this legislation, FAME is now prevalent across the UK fuel market – both at the pump and within red diesel (class A2).
2# How does FAME affect my organisation?
FAME’s unique properties have a dramatic impact throughout the fuel supply chain; from vehicles and machinery to storage tanks and transport.
Understanding FAME’s Chemical Properties
As a powerful solvent, FAME dissolves a wide range of chemical surfaces which would be unaffected by FAME-free fuel oils. This can result a wide range of material compatibility issues throughout the fuel supply chain. FAME has been found to dissolve many common rubbers, plastics and surface coatings!
FAME’s hydroscopic property means it readily absorbs moisture from its surroundings. Unlike regular diesel which tends to shed water to the bottom of the tank, FAME absorbs the water throughout the fuel. This biologically rich environment encourages the growth of microbes, mould and bugs throughout FAME blended fuel.
The potential for microbial growth and high water content results in a number of common problems
Common Issues
- Line and filter blockages – from residual deposits
- Fuel stability issues – FAME degrades over time, through oxidation and hydrolysis
- Poor cold weather performance – cold flow waxing and precipitation
- Shortened shelf life
3# Avoiding the negative impacts of FAME
There are a number of best practices when storing, transporting or combusting fuels which contain FAME components.
We recommend the following actions
- Any equipment which is routinely exposed to FAME should be made from FAME compatible materials. This applies throughout the fuel supply chain – including tanks, vessels, pumps, filters, piping, fittings, gaskets, hoses and instruments.
- It is vital to prevent water and sediment contamination – as this will accelerate the spoiling of fuel stock.
- Filter locations, sizes and frequency of changes should be reviewed. Thanks to FAME’s high solvent properties, sediments and microbial deposits can be redissolved.
- Fuel temperature should be kept above its cloud point – to minimise the chance of solids dropping out and resulting in clogging issues.
- Stock management and storage systems are crucial when dealing with these fuel products. See more information below.
- A range of fuel additives claim to reduce the blocking and clogging frequently resulting from fuels containing FAME. Ensure additives are applied at the correct proportions and to manufactures recommendations.
For some applications, it is possible to use fuels that contain reduced or zero levels of FAME, and therefore avoid the problems mentioned in this article. Visit HVO or Specialist Heating Oils for more information on FAME free fuels.
4# Storing fuels containing FAME
The storage management of FAME containing products is crucial. Whilst traditional lifecycle storage is recommended as a maximum of 6 months, this is based on ideal storage conditions. With the introduction of increased FAME levels, there is an increased incidence of fuel contamination, water ingress and associated issues.
It is vital that businesses implement a rotating stock management system to prevent excessive storage periods.
In a high fuel throughput environment, stock levels should be sufficient to maintain operability, whilst preventing water ingress. Where there is limited fuel throughput, minimise the fuel stock where possible and implement fuel quality testing periodically. When fuel storage is not being used, ensure the tank is kept empty until required.
What if my fuel is not used within the advised timeframe?
If product is not used within the recommended timeframe, we recommend the following:
- Test the fuel quality before you use it.
- Confirm if contamination of separation has occurred by dipping your tank.
- If so, drain bottom of the tank until clear product is visible.
- Before using the fuel, replace the inline filters in your fuel system.
Should you find the fuel is contaminated, the product should be removed, the tank cleaned and refilled with clean product.
5# Living with FAME
New legislation is set to substantially increase the proportion of FAME in both red and white diesel throughout the UK. If left unmanaged, this increase in bio-content will result in more frequent plant down-time, unexpected maintenance costs, and the disposal of contaminated fuel products.
Those organisations who take steps to manage stock levels, prevent water ingress, and ensure material compatibility (alongside the other recommendations above) are best placed to avoid the pitfalls of these FAME levels.
If you would like any further assistance managing fuels containing FAME or would like to discuss FAME free fuels, get in touch here.